For every new stone mason, seven retire: St Paul’s plan to save heritage crafts — and itself in the process
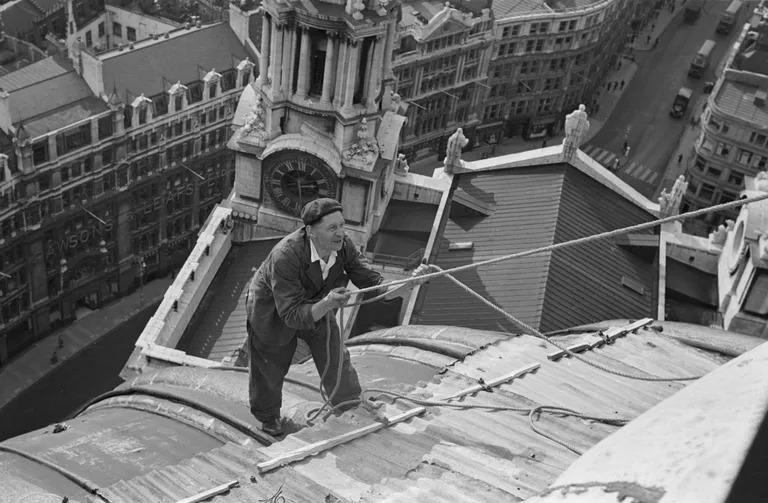
As St Paul’s Cathedral launches the Wren Centre of Excellence to train young people to repair Britain’s historic buildings, Lotte Brundle talks to restoration workers about why their industry is on a cliffs edge.
St Paul’s Cathedral is an icon of the London skyline — as much as the Shard, the London Eye, Big Ben and that building with the three fans that are mysteriously never spinning. Wherever you go, you can’t help but notice its looming spire and majestic dome. However, it has taken a lot of work to keep it looking that way and the cathedral has undergone many restoration projects over the years.
On Christmas Eve, in 1924, St Paul’s was served with a Dangerous Structures notice and closed for safety reasons after the building moved and cracked, causing masonry to fall and collapse, smashing into the nave. During the Blitz, disaster struck again, twice — with one bombing in 1940, the other in 1941. It was also severely damaged in the Great Fire of London in 1666, two years later the nave fell victim once more, suffering a total collapse. In 2011, Londoners may remember when the scaffolding which had been omnipresent around the structure for 15 years, hiding its ethereal beauty, finally came down, as an all-encompassing restoration projection came to fruition. This included the addition of wheelchair access to the crypt. More recently, in 2023, the cathedral received a grant of a whopping £500,000 to help restore its seven meter tall cupola, ball, and cross (for the uninformed, that’s the small spindly bit right on the very top).
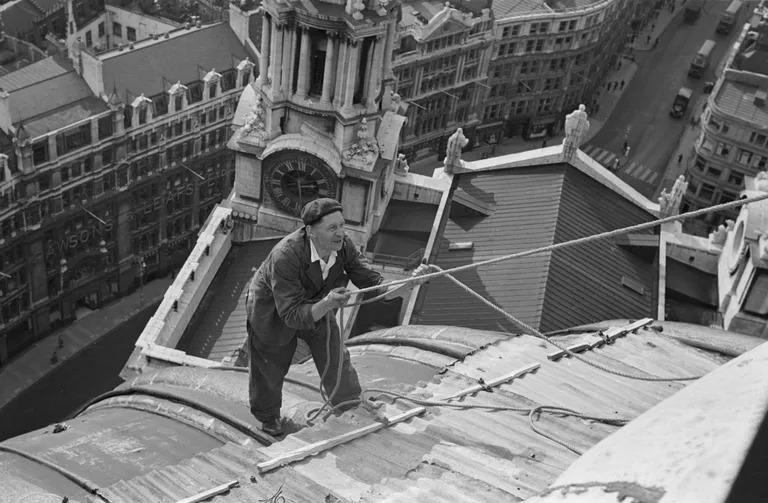
A lot of people, a lot of time and a lot of money have gone into keeping St Paul’s spectacular, and the institution, which welcomes more than a million visitors a year, is anxious that these works continue. Currently for each new heritage carpenter or stonemason trained, seven retire — odds that aren’t in the interest of Britain’s oldest buildings. This is why they are launching a new centre which will run apprenticeships in stonemasonry and carpentry. Named after its architect, Sir Christopher Wren, the Wren Centre of Excellence’s opening coincides with the 350th anniversary of the foundation of the cathedral and promises to be a ‘world-class hub for heritage craft training and innovation’.
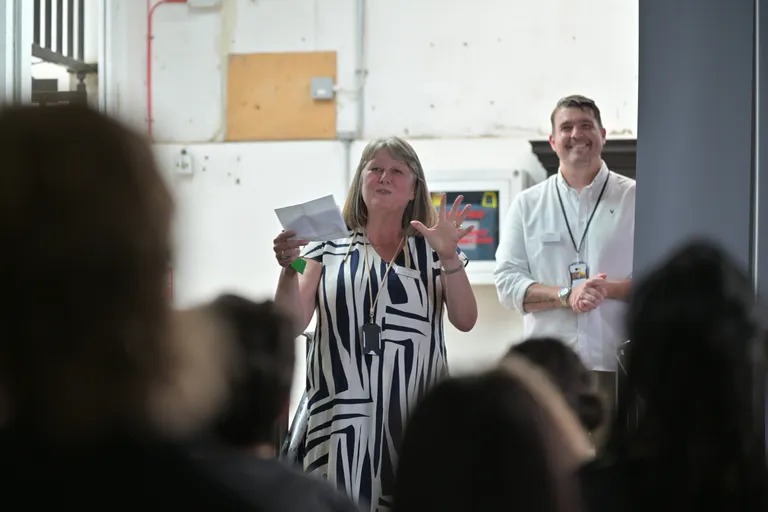
Rebecca Thompson came to St Paul’s two years ago, and the project is partly her ‘brain child’, inspired by the team that works there. The director of property realised that a number of the staff were hoping to retire in the next couple of years which got her thinking. ‘The concern was, how do we make sure that the skills that we’ve got can then be transferred to the next generation of carpenters and stonemasons that will come and work at St Paul’s for the future projects, because the skills that the team have got are much wider and more complex than anything that is taught in college,’ she said. ‘Very quickly, we decided we needed apprentices.’
Joe Gallagher, 62, is a carpenter at St Paul’s. He, along with colleague James Digger, 26, a stone mason with an apt surname, both got into their line of work through similar apprenticeships when they were 16. ‘The variety,’ Digger says reflecting on his apprenticeship, ‘that’s the best thing about it.’ Since Gallagher graduated from his apprenticeship scheme, some 46 years ago, he’s worked on a variety of projects, from carpentry for the Royals, to The National Trust. ‘I never thought I’d be working at St Paul’s, I must admit,’ he tells me. By the time the new apprentices are trained he will be retired. ‘I’m hoping someone will learn from us, and that they will continue the standards that we’ve set,’ he reflects. ‘Hopefully they will be successful too — find something that they enjoy.’
‘It’s always been unusual to do,’ says Sam Lee, the director of London Stone Carving. He thinks the Wren Centre sounds ‘like the dream college’; he studied stone masonry during his Bsc in Building Conservation at Weymouth College in Dorset. ‘They’ve since closed, as have several other stone masonry colleges around the country,’ he tells me. ‘That one was purpose made and only a few years old when it closed, so there’s a lot of challenges when it comes to the stone industry, especially now.’ He tells me that the proof today that the various elements of the job are detrimental to people’s health — the vibration of tools resulting in breathing in dust, as well as the heavy lifting involved — means it’s increasingly becoming mechanised, ‘which means the standard of everything is going down because there’s no sort of human interaction with the things that are being made’.
As well as health concerns, another barrier to getting young people involved is awareness. ‘You only do it if you’ve heard of it,’ says Lee, whose family historically built churches. Digger also had initial concerns about who would be interested in the apprenticeship. ‘I wouldn’t say it’s particularly dangerous, but there is an element of manual labour to it,’ he says. ‘It’s never particularly back breaking — or, if it is, it’s for a short period of time — but you always work out how best to do that safely, and as a team, but I was quite worried, before this [apprentice open day] event that we had on Wednesday. I’ve got some friends in various sectors of the construction industry, and they said they’ve done some events with hundreds of students, and that they could probably only pick out a handful of ones that would even pick up the tools to give it a go.’